We’ve got news about an acquisition and a collaboration to start off today’s 3D Printing News Briefs, before moving on to two stories about additive manufacturing software. Then there’s a story about a grant for heat exchanger design, a milling head that integrates into a 3D printing solution, and interesting 3D printed hook and loop fasteners. An aquaculture business has 3D printed an oyster tank made of wood.
GoEngineer Acquires rapid PSI to Expand its 3D Printing Capabilities
Rapid PSI is a Kansas-based service bureau that specializes in 3D printing. GoEngineer has acquired Rapid PSI to expand its 3D print capabilities. By pairing GoEngineer’s varied portfolio of engineering solutions, which includes CAMWorks, Stratasys, and SOLIDWORKS, with Rapid PSI’s reputation as a leader in supply 3D printed parts, the industry will enjoy increased access to 3D printing expertise and capabilities, such as customized solutions, prototyping, and production-grade printing. RAPID PSI’s office and team in Wichita will continue to serve the region.
“We see great potential in joining forces with GoEngineer and leveraging their extensive resources and network. Together, we will be able to offer even more advanced 3D printing solutions to our clients, helping them revolutionize their product development processes,” said Phil Nettleton, President of Rapid PSI.
flō Collaborating with Weizmann Institute of Science on Advanced Optical Materials
Israeli startup flō is collaborating with Yeda Research and Development Co., Ltd., the commercial arm of the country’s prestigious Weizmann Institute of Science, having signed an exclusive license agreement to use Weizmann Advanced Materials for ophthalmic coatings applied with its own proprietary AM technology. The manual coating of optical lenses, which can be used for a variety of purposes, is costly and time-consuming. Plus, since it’s an analog process, it’s hard to achieve repeatability, which then results in defects. But a digital process using flō’s multi-material, multi-layered optical coatings makes it possible to accurately control coating down to the micro level, offering improvements in cost, functionality, sustainability, quality, and more.
“We are humbled by this partnership. The Institute’s vast know-how regarding advanced materials in optics, coupled with its amazing academic talent, gives us unprecedented access to innovation resources. We have the advanced technology, staff, and the right partnerships in place – a recipe for success,” said flō’s CEO & Chairman Jonathan Jaglom.
Mastercam introduces new software add-on for additive manufacturing
Mastercam, the leading CAD/CAM product, has announced a new additive manufacturing add-on. Mastercam APlus is a new add-on product from CAMufacturing Solutions that uses the same interface as Mastercam Mill, Lathe and Router users are used to. It allows customers with Mastercam Mill Lathe Router licenses the ability to backplot and simulate 3D print scenarios in the same way. The addon is based on Direct Energy Deposition, integrates seamlessly into Mastercam, has toolpaths that are specifically designed for AM geometry and includes features and utilities to increase efficiency and remove any uncertainty in the process. The new Mastercam APlus add-on by CAMufacturing Solutions is now available for purchase through Mastercam’s worldwide reseller channel.
“APlus brings Additive Manufacturing to the Mastercam user in a form that is consistent with the workflow used for over 40 years,” said Kenneth Fortier, Technical Product Manager, Mastercam. “Direct Energy Deposition is making its way into many machine shops and being able to program hybrid machines or dedicated additive machines using Mastercam makes the transition seamless. With the hybrid process of alternating adding material and milling allows parts with internally machined features to be created that would have been impossible without additive.”
Trumpf’s 3D Printing Software Saves Material with No Support Structures
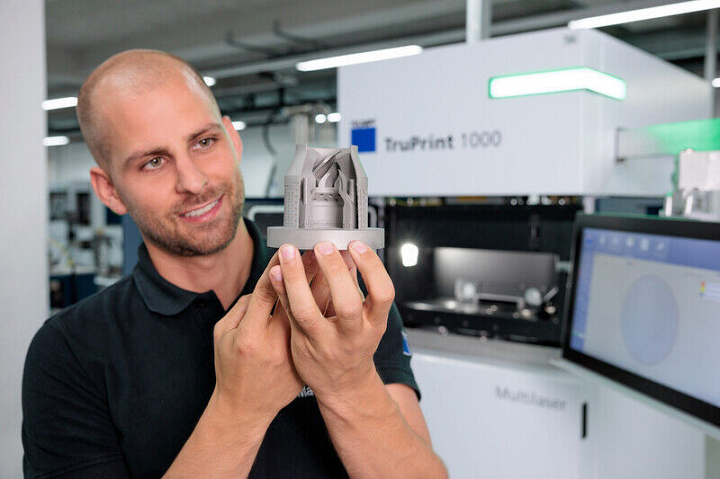
Trumpf has developed a software for metallic 3D printing that allows many components to be manufactured additively without any support structures.
At the recent EMO Hannover 2023 trade fair, Trumpf showcased an improved version of its Trutops Print software, which allows users to fabricate metal components with extreme overhangs of up to 15° without using support structures. The new functions are time and material efficient, and allow the creation near-net shapes, such as internal cooling channels of large diameters. Support-free 3D Printing is useful for many industries, especially when creating parts with large cavities or tricky overhangs, like hydraulic blocks, tanks and tool inserts used in plastic injection molding. It’s also possible to print without support structures in many cases even when you’re using materials that are hard to process, like stainless steel.
Trumpf wants to control precisely when and where the material will be liquid, then become hard again, during 3D printing. This is achieved by using the proper exposure strategies in order to avoid residual stresses and overheating at the overhang. The Trutops Print software enhances the capabilities of the printer. It uses the best strategy to expose different areas of the prints, so support structures are rarely needed. Trumpf 3D printers with improved gas flows also allow users to achieve uniform conditions for the process. The heat from exposed parts is dissipated to prevent component distortion due to internal stresses.
TOffeeAM & Imperial College London Awarded Grant for Next-Generation Heat Exchangers
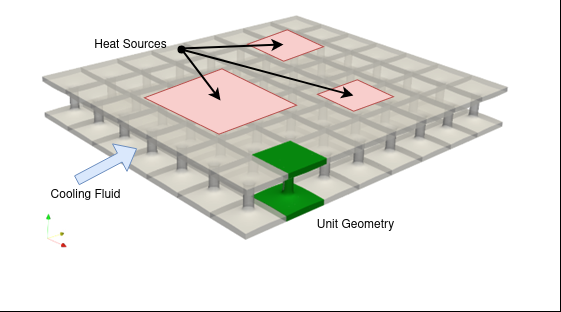
Schematic representations of the Multi-Scale Approach
Imperial College London and TOffeeAM have won a grant through InnovateUK. InnovateUK is part of the non-departmental UK Research and Innovation body (UKRI), whose mission it is to drive productivity and economic growth in businesses by helping them develop and realize innovative ideas. The grant will go towards an exciting and ambitious project, “Multiscale Optimization Framework for the Next Generation of Heat Exchangers.” It’s focused on developing an alternative design framework for cold plates, which could revolutionize thermal efficiency, and aims to provide engineers with the ability to create heat exchanger designs that are above and beyond the traditional “serpentine” solutions—instead requiring less pumping energy to operate and offering superior heat transfer.
TOffeeAM develops generative design software for engineering components, and will use cutting-edge multi-scale methods pioneered by researchers in Imperial College London’s Department of Aeronautics during the 14-month project. Market share for exchangers could reach $26.26 billion in 2030.
XtreeE introduces Advanced Milling Integration Option
XtreeE’s technology platform, which aims to improve construction productivity and create a low carbon living environment, allows architects, engineers and product designers, as well as project owners and construction firms, to design and manufacture optimized building and infrastructure components using its large-scale robotic 3D printing solution. The company has developed a hybrid technology that integrates a new, advanced milling solution directly into their 3D printing solutions. The switchover between 3D-printing and milling is quick, taking only five minutes. A new milling tool can also be used to polish and texture 3D printed objects for an outstanding finish.
In response to a comment on its LinkedIn post sharing the news, XtreeE replied, “XtreeE’s vision is all about delivering certified finished products that work as both permanent formworks and structural elements. Here, the key is to eliminate risky on-site alterations by making assembly simple and precise. This not only boosts safety but also ensures top-notch quality and cost savings in construction.”
3D Printed Velcro…Hook and Loop Fasteners
Velcro is a trademark, so we’ll call this cool project that Hackaday writer Al Williams highlighted by its actual name: 3D printed hook and loop fasteners. Michael Laws, an industrial designer and primary/secondary school teacher, investigated 3D-printed fasteners in his latest Teaching Tech YouTube video. He explored the models available on Printables, and converted his favorite design into a fully parametric OpenSCAD version. Michael Laws began by explaining the 3D-printed version of Velcro and its function. He then investigated the best material for 3D printing hook-and loop fasteners. Laws tried out PLA, TPU, and PETG, and after strength testing, found that the latter was the best option, with what Hackaday described as a “surprisingly robust” bond. This project was made easier by the stringing in the print.
“Some of the designs were rather large, like we would have expected. However, some of the designs were fairly small and looked almost like real Velcro,” Williams wrote. “However, since the pattern is not as random as the fabric portions of the real deal, it seems like alignment between parts is more critical when you are joining the two halves.”
Aquaculture: Wooden Oyster tank 3D printed
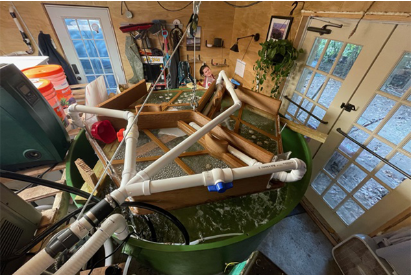
New Maine oyster farm Muddy River Farm Aquaponics will be using a revolutionary new tank for its oysters, one made of 3D printed wood.
Muddy River Farm Aquaponics in Maine is finally opening a new facility that uses solar power and a 3D-printed wood tank to grow oysters. They are also aiming to produce healthy freshwater fish and vegetables at low cost. MRF’s Matt Nixon, who is a PhD candidate in the University of Maine and has worked for the state for 11 years, studied different aspects of sustainable fishing, and observed how the warming waters adversely affected the water-related industry. Matt Nixon, a PhD candidate at the University of Maine, spent 11 years working for the state, looking at various aspects of sustainable fisheries, and noticed how warming waters negatively affected different water-related industries. He decided tanks would be the best way to grow oysters, but the typical ones made from glass, steel, or concrete were too costly. A colleague suggested that he try 3D printing, and since the university is home to one of the world’s largest polymer printers, in addition to having a cooperative agreement with the US Department of Energy to find new 3D printing applications, it was a perfect match.
Nixon and his team developed a patent-pending prototype design, 3D printed out of biodegradable lumber scraps and waste, that won’t degrade in salt water. It’s a plug-and-play, vertical, closed loop system with constant water flow, and the whole tank structure, which consists of six stacked hexagons, measures about 8′ x 8′. The tank requires very little electricity and oysters can reach near-market size inside five months as opposed to taking three years to grow in the ocean. MRF is able to produce 20,000 oysters in each array without having to wait for the ideal water temperature. Nixon plans to license the technology, so the wood tanks can be 3D printed and deployed around the world, even where there’s no water; he says that ideally, someone could even “get a lease for an aquaculture site to grow oysters in their garage.”
Subscribe to Our Email Newsletter
Receive information and offers about 3D printing from third-party vendors.